Lean Change Management – Produktionssystem und Selbstmanagement
Produktionssystem als Bestandteil von Selbstmanagement
Lean-Management steht für „Vermeidung von Verschwendung“. Der Ursprung des Lean-Managements liegt im Produktionssystem von Toyota.
Der Begriff „Lean Manufacturing“ wurde erst 1988 geprägt. Toyota begann aber bereits in den 1930er Jahren mit der Entwicklung von Lean-Methoden zur Abfallbeseitigung (Ursprung des Lean-Managements liegt im Produktionssystem von Toyota. Japans Kultur ist von einer großen Hochachtung gegenüber der Perfektion von Prozessen geprägt).
Das Toyota Production System (TPS), bildete bereits in den 1950er Jahren die Grundlage für eine moderne Lean Produktion. TPS wurde vom Fertigungsleiter Taiichi Ohno (1912-1990) ab Mitte der 1950er Jahre entwickelt und jahrzehntelang verfeinert.
1992 übernahm die Adam Opel AG als erster deutscher Hersteller die Lean- Methoden des Toyota Production System. Darauf folgten Mercedes-Benz, MAN, Audi und Volkswagen. Danach folgten immer mehr Zulieferbetriebe und Unternehmen weiterer Branchen.
Der Fokus liegt auf den beteiligten Menschen. Verschwendung zu vermeiden ist ein wesentlicher Bestandteil der Wertschöpfung. Dennoch ist nicht beabsichtigt die Wertschöpfung/Verschwendung mit dem Grad der Wertschätzung für die Leistung/Arbeit der jeweiligen Mitarbeiter zu vermengen.
Verbesserung und Innovation erfolgen nur dann, wenn den Mitarbeitern die Freiheit überlassen wird, diese selbstorganisierend zu implementieren. Dieser Grundsatz macht Lean Change Management sowohl für das Thema New Work, als auch Selbstmanagement interessant.
Details zum Thema „Selbstmanagement“ findest Du in meinem Artikel „Selbstmanagement – Basis für Erfolg“.
Die 7 Arten der Verschwendung in der…
…Produktion
- Überproduktion
- Bestände
- Transport
- Unnötige Prozesse
- Wartezeiten (Menschen, Maschinen)
- Fehler/Nacharbeit/Ausschuss
- Bewegung
…Verwaltung
- Überproduktion von Informationen
- Fremd verursachte Bestände von Information (elektronische oder physische Bestände)
- Transport von Information
- Unnötige Prozesse (im Arbeitsprozess selbst, nicht angemessene Methode)
- Wartezeit von Mitarbeitern
- Fehler/Nacharbeit (Produktion von ungenauen oder falschen Informationen)
- Bewegung/Laufwege im Büro
3 Tools des Lean Manufacturing
5S-Methode
Grundlage für ständige Verbesserungen in allen Abteilungen in Verwaltung, Entwicklung und Produktion.
S1 = Sortieren
- Sortieren im Sinne von Aussortieren
- Alles vom Arbeitsplatz entfernen, was für die Durchführung der Arbeit nicht benötigt wird. Mehr Platz für die tatsächlich benötigten Arbeitsmittel und Materialen. Mehr Übersichtlichkeit am Arbeitsplatz.
S2 = Systematisieren:
- Jedes Dinge am Arbeitsplatz hat seinen Platz (nur einen). Dieser wird entsprechend markiert (Visualisierung durch z.B. Schattentafeln, Bilder des Soll-Zustandes, um Abweichungen erkennen zu können).
- Die Anordnung von Werkzeugen und Materialien erfolgt in Abhängigkeit ihrer Verwendungshäufigkeit und/oder Verwendungsreihenfolge
S3 = Säubern:
- Arbeitsbereich regelmäßig säubern und dabei inspizieren (auf Defekte, Abweichungen, Fehlen von Dingen).
- Positiven Außenwirkung durch Sauberkeit und Sortierung aller Dinge.
S4 = Standardisieren:
- Standards in allen Bereichen (z.B. Farbcodes für Wegbegrenzungen, Abholflächen, Anlieferungsflächen; Bilder für Soll-Zustände; Reinigungspläne; Checklisten zur Überprüfung von Abweichungen von den Standards und der 5SMethode etc.)
S5 = Selbstdisziplin & ständiges Verbessern:
- Regeln für Ordnung und Sauberkeit!
- Kontrollen, um Abweichungen vom Standard festzustellen
- Abweichungen verhindern und abstellen
Ziel ist es, Arbeitsplätze zu schaffen, an denen Produkte in bester Qualität, in kürzester Zeit und mit höchster Sicherheit erstellt werden.
Folgende Vorteile ergeben sich durch die 5S-Methode:
- Verschwendungen werden erkannt —> können eliminiert werden.
- Ein ergonomischer und sicherer Arbeitsplatz wird geschaffen —> erfordert kürzere Einarbeitungszeiten
- Produktivität wird erhöht; Störungen verringert —> Mitarbeiter fühlen sich wohl am Arbeitsplatz.
- Vorbereitungs- und Rüstzeiten werden verringert —> die Verfügbarkeit der Maschinen wird erhöht.
- Die Qualität wird erhöht, Reklamationen werden verringert —> Vertrauen des Kunden wird erhöht.
- Flächen werden besser genutzt —> Produktiver aber auch vorzeigbar für den Kunden.
- Erfolge werden visualisiert —> verbessert das Gemeinschaftsgefühl.
- Arbeitssicherheit —> Ordnung + Sauberkeit = positiver Effekt auf Arbeitssicherheit.
Gemba
„Gemba Walks“: Kommunikation zwischen Produktion und Unternehmens-Leitung. Verständnis von Problemen entwickeln, die die Produktion betreffen, wie z. B. Fähigkeiten der Arbeitnehmer, Leistung der Ausrüstung und Materialhandhabung. Gemba dient weniger der Kontrolle der Mitarbeiter, sondern der Absicht, dass sich die Unternehmens-Leitung aller Abläufe in Verwaltung und Produktion vertraut machen muss, um überhaupt realistische Entscheidungen fällen zu können. Wer nur die klassischen Kennzahlen seines Unternehmens kennt, wird nie in der Lage sein, die Möglichkeiten eines Unternehmens und seiner Mitarbeiter zu erkennen.
Kaizen
(Kai = Veränderung; Zen = zum Besseren; Kaizen = kontinuierlicher Verbesserungs-Prozess (KVP), Continuous Improvement Process (CIP) = Verschwendung vermeiden)
- Übernahme von Gemba-Praktiken
- Feedback von Mitarbeitern zu den täglichen Prozessen (Gerätestatus, Arbeitsplatzatmosphäre etc.)
- Produktion im Blick haben, um Verbesserungen zu ermöglichen
- Bezüglich technologischer Fortschritte immer auf dem Laufenden bleiben
- Produktion verbessern
- Die erreichten Verbesserungen müssen als neue Standards eingeführt und gefestigt werden. Es gelten dabei die folgenden Prinzipien:
- Standards dienen der Erhaltung des Erreichten.
- Ein Standard gibt Aufschluss über die übertragenen Aufgaben.
- Standards müssen ständig nach PDCA verbessert werden.
KaiZen macht nachhaltigen Erfolg möglich
Nicht die sprunghafte Verbesserung durch Innovation, sondern eine schrittweise erfolgende Perfektionierung führt zum Erfolg.
Projekt-Innovation versus Kaizen = kontinuierlicher Verbesserungs-Prozess (KVP)
Die Philosophie des KaiZen beabsichtigt nicht die sprunghafte Verbesserung durch Innovation, sondern eine schrittweise erfolgende Perfektionierung. Dies führt zu kleinen, aber stetig inkrementellen Verbesserungen.
Der Kunde steht deutlich im Mittelpunkt.
Es wird aus Sicht des Kunden gehandelt und entwickelt.
Customer Centricity ist ein wichtiger Teil der Wertschöpfung.
Der Kunde definiert den Wert.
Nur was der Kunde wirklich bereit ist zu bezahlen, hat Wert.
Lean – Vermeidung von Verschwendung
Da es beim Selbstmanagement, um Übersichtlichkeit, Zufriedenheit und Fokus geht, bieten sich im Lean passende Methoden, insbesondere hinsichtlich der Vermeidung von Verschwendung.
Insbesondere im Büro erleben wir alle regelmäßige Verschwendung:
- Wer im Büro arbeitet, wird regelmäßig unterbrochen – oder unterbricht sich selbst.
- Viele benötigen im Durchschnitt 7-11 Minuten, einige bis zu 23 Minuten, um wieder in den Fokus der eigentlichen Arbeit zu kommen.
- Arbeitnehmer verbringen bis zu 1 Jahr ihres Lebens in Meetings. Im öffentlichen Sektor fast 2 Jahre.
- Arbeitnehmer verbringen 1 Jahr Ihres Lebens auf dem Weg zur und von der Arbeit. Bei Gesamtkosten von ca. 60.000 Euro.
- Arbeitnehmer verbringen 4 Jahre ihres Lebens mit E-Mails.
- Nur 14% der Arbeitnehmer möchten in Zukunft in einem traditionellen Büroumfeld arbeiten.
Verschwendung im Büro – Zeitverlust bei folgenden Tätigkeiten:
- Suchen von Unterlagen, Dateien, Informationen…
- Unterbrechungen während der Arbeit…
- Warten auf Kollegen, Unterschriften, EDV Programme…
- Aussortieren von Informationen, die man erhält ohne sie zu benötigen…
- Transportiere von Papier-Dokumenten von/zum Kopierer, Hauspost etc…
- Teilnahme an ineffizienten Meetings…
- etc.
Was ist Wertschöpfung?
Der Kunde steht deutlich im Mittelpunkt.
Es wird aus Sicht des Kunden gehandelt und entwickelt.
Customer Centricity ist ein wichtiger Teil der Wertschöpfung.
Der Kunde definiert den Wert.
Nur was der Kunde wirklich bereit ist zu bezahlen, hat Wert.
Alle Tätigkeiten an einem Produkt/Dienstleistung, die den Wert des Produktes/Dienstleistung aus Kundensicht steigert, z.B.
- Funktionalität optimieren (Bedienbarkeit vereinfacht)
- Erreichbarkeit optimieren (Kunden-Dialog vereinfacht)
- Arbeitsplatz aufgeräumt (alles besser finden, Ablenkung vermeiden)
- Produktion-Prozesse verbessern (das Produkt wird besser und/oder kann günstiger hergestellt werden)
Was ist Verschwendung?
Alle Tätigkeiten, die den Wert des Produktes/Dienstleistung aus Kundensicht nicht erhöhen.
- Die Problematik der Verschwendung ist weniger deren Beseitigung, sondern viel mehr deren Erkennung und Wahrnehmung.
- Verschwendung muss zuerst erkannt und auch als solche akzeptiert werden, damit sie reduziert und/oder eliminiert werden kann.
Lean Management nutzt den Anspruch auf kontinuierliche Verbesserung als Basis zur Vermeidung von Verschwendung. Wobei die Vermeidung von Verschwendung die Verbesserung erst ermöglicht.
Es ist beabsichtigt, Prozesse möglichst zu standardisieren und zu vereinfachen, bis nur noch jene Elemente übrig sind, die wesentlich zur Wertschöpfung beitragen.
Ziel 1 —> Suche nach Kostenvorteil gegenüber dem Wettbewerb.
Ziel 2 —> Zufriedenheit des Kunden.

Prinzipien von Lean
- Mache nur die Tätigkeiten, die Werte für alle schaffen
- Ermächtige die „Leute vor Ort“
- Reagiere unmittelbar auf Kunden und die „Leute vor Ort“
- Optimiere den Ablauf (Flow) basierend auf Anforderung und Hypothesen (Pull)
Das Besondere an Lean Change
- Statt Experten => Jeder macht Lean Change!
- Statt Expertenwissen => Learning by Doing!
- Statt ausschließen => Jeden einbinden!
- Statt Pläne => Experimente machen!
- Statt Vorabplanung => iteratives und inkrementelles Vorgehen mit schnellen Feedback-Schleifen
Lean Change Management…
…ist ein dauerhafter Prozess zur Veränderung!
…ist kontinuierliche Verbesserung auf dem Weg zur Lernenden Organisation.
„Making money is good.
Making a difference is better.
But making money while making a difference beats all…“
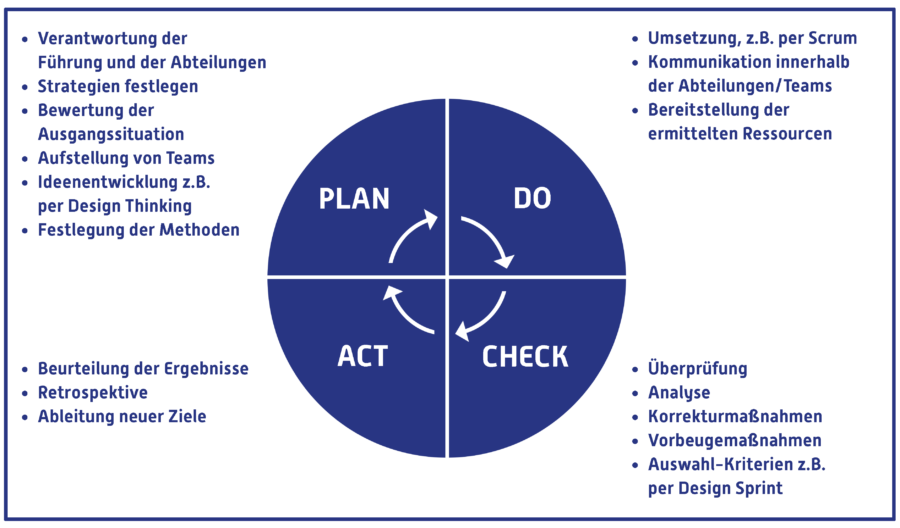
Als Ergänzung empfehle ich Dir meinen Artikel „Selbstmanagement – Basis für Erfolg“.
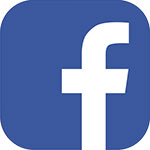
Schließe Dich unserer Facebook-Gruppe an:
„Erfolgreich – mit Methode und Selbstorganisation – Life & Business Design“
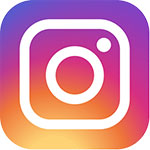
Folge mir auf Instagram @life.business.design
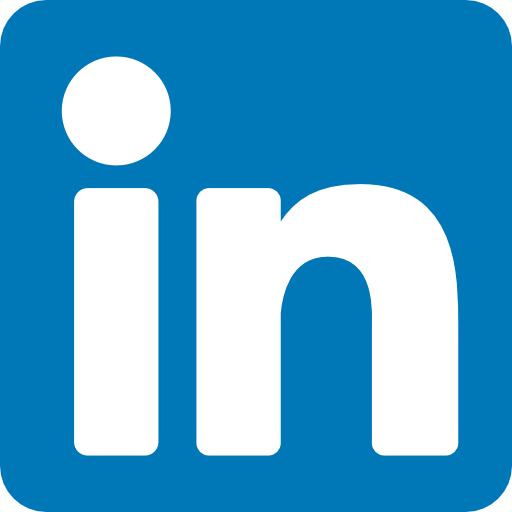
Folge mir auf LinkedIn
Wendest Du Lean Change Management an?
Schreib mir in den Kommentaren.